The possibilities that a breakthrough technology brings to an established industry can be difficult to identify. Because true breakthroughs don’t just improve what already exists; they open up new worlds of possibility, changing the very nature of what can be accomplished, planned, or even imagined.
At the recent SAE International WCX Digital Summit, p-Chip Corp. CTO Bill Eibon helped bring to light one such world of new possibility for the automotive industry. Eibon’s presentation provided thoughtful insight into the incredible track & trace capabilities now available for the serialization of integrated circuits, safety components, and electronic systems.
Thanks to rapid advancements in light-activated microtransponder technology, the game is changing for forward-looking automotive manufacturers. To learn how, have a listen, or read the transcript below:
Transcript of the Presentation
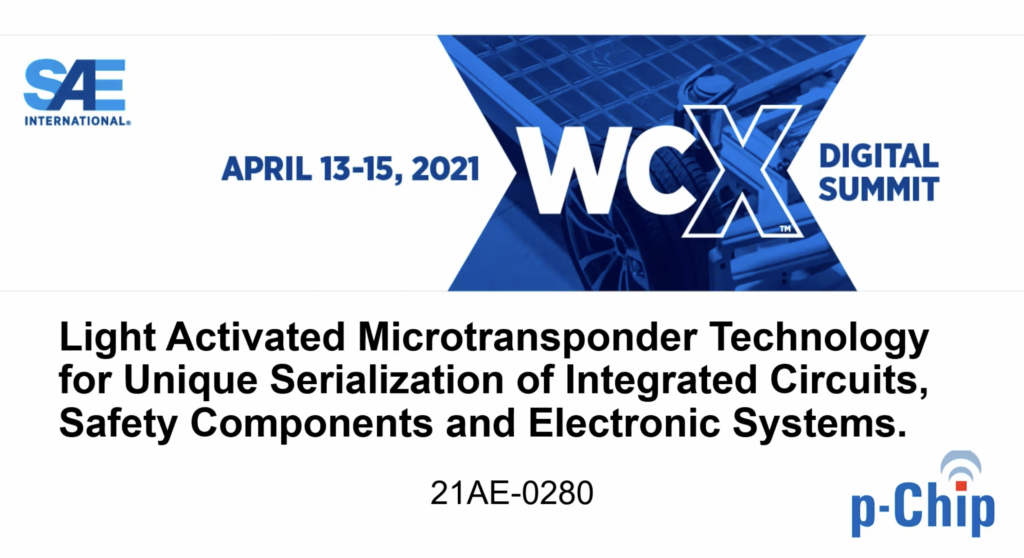
Hello, my name is Bill. I’m the Chief Technology Officer of p-Chip. I’m a material scientist with 35 years of automotive experience from new product r&d through manufacturing, to direct assembly line support on a global scale.
I want to introduce to you a little known biological technology that is poised to positively disrupt industrial track and trace capabilities. This technology can improve transparency, safety and performance at an affordable cost to serve.
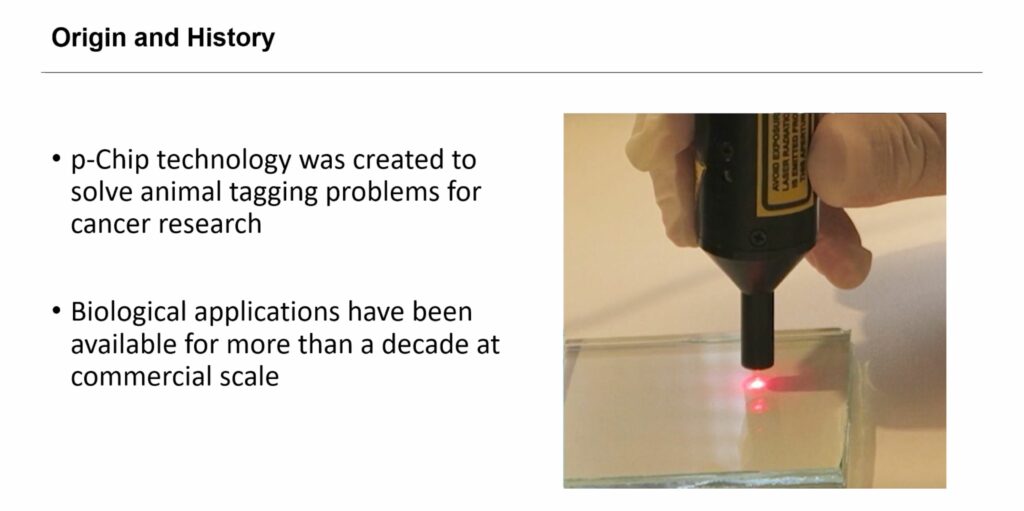
Like all great inventions, p-Chip microtransponders were invented to solve a problem. Lab mice with specific gene expressions are very expensive and can cost more than $40,000 US apiece. During cancer research, these mice would destroy their ear tags, rendering years worth of data and millions of dollars worth of research unusable.
A simple, low-cost and super reliable digital tagging technology was needed and subsequently developed. Over the last decade, the technology has been commercially scaled and demonstrated to be reliable.
I’m sharing this background with you because the benefits of meticulous development for biological applications have generated highly advantageous digital track and trace solutions that are very relevant for the transportation industry.
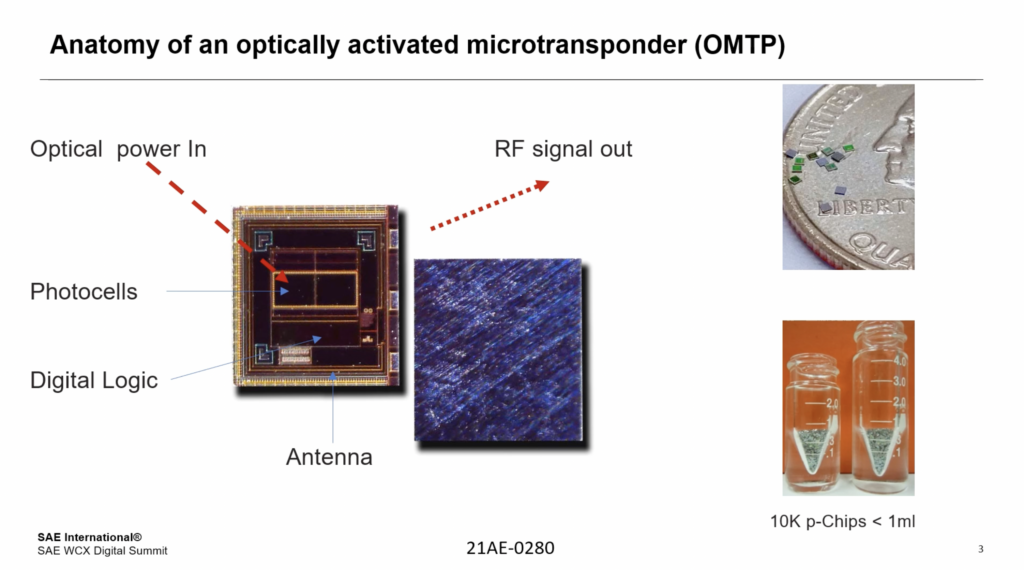
At the wafer level, p-Chip microtransponders are produced using standard, high-volume integrated circuit processing and equipment. The p-Chip microtransponder itself is a passive taggant, and it’s activated by light. Light-activation energy can be visible through infrared. The output signal from the p-Chip microtransponder’s radio frequency low volume is referred to as an optically activated microtransponder.
So while the structure itself has more than 20 discrete layers, the key features shown here include your
- multiple solar cells
- digital logic area
- antenna structure and
- a transponder
So, when the correct wavelength of light from the proper frequency modulation hits the p-Chip microtransponder, energy harvesting starts and the chip enters the active state. The chip sends low energy encoded radio frequency signals back to the reader. The unique serial number on each chip is part of the physical integrated circuit. It’s not temporary; it’s not programmable memory that can be changed or modified. Any attempts to modify the ID number will destroy the chip.
The chip doesn’t have an onboard clock, enabling it to be very small. As you can see in the pictures on the right, dimensions of the p-Chip microtransponder are roughly 500 microns square and 100 microns thick.
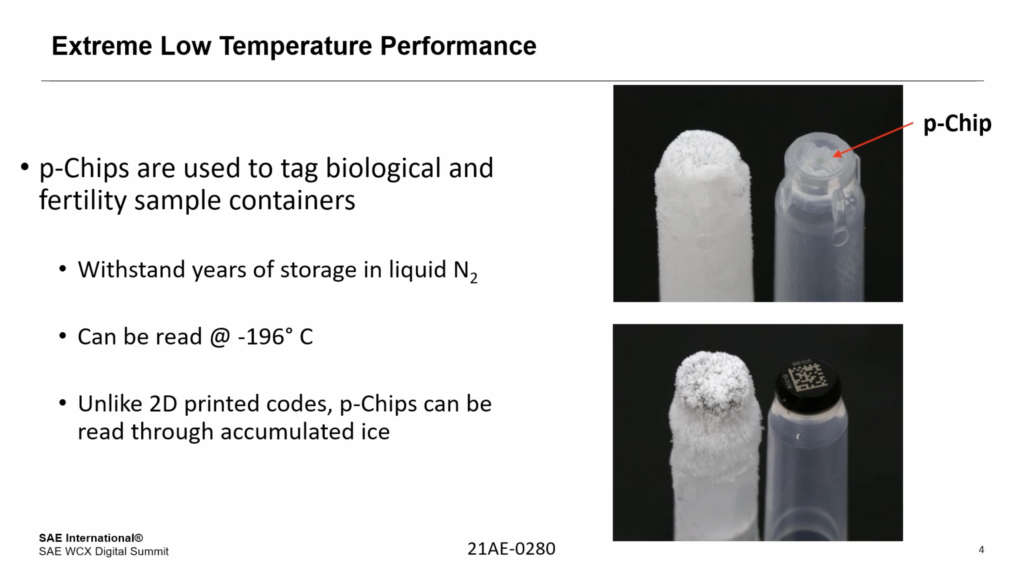
p-Chips are used to tag biological and fertility sample containers. They’re routinely stored for years on end, in liquid nitrogen. They can actively be read at liquid nitrogen temperatures; they don’t need to be warmed up to be read.
The pictures that you see on the right show another advantage, and that’s the ability to read through ice. So the p-Chip microtransponder on top can be read through the ice formation. When you look at the QR code on the bottles on the bottom, they can’t be read and neither can the barcode. So this is a really important advantage.
Requirements of biological sample storage far exceed low temperature specifications for automotive systems.
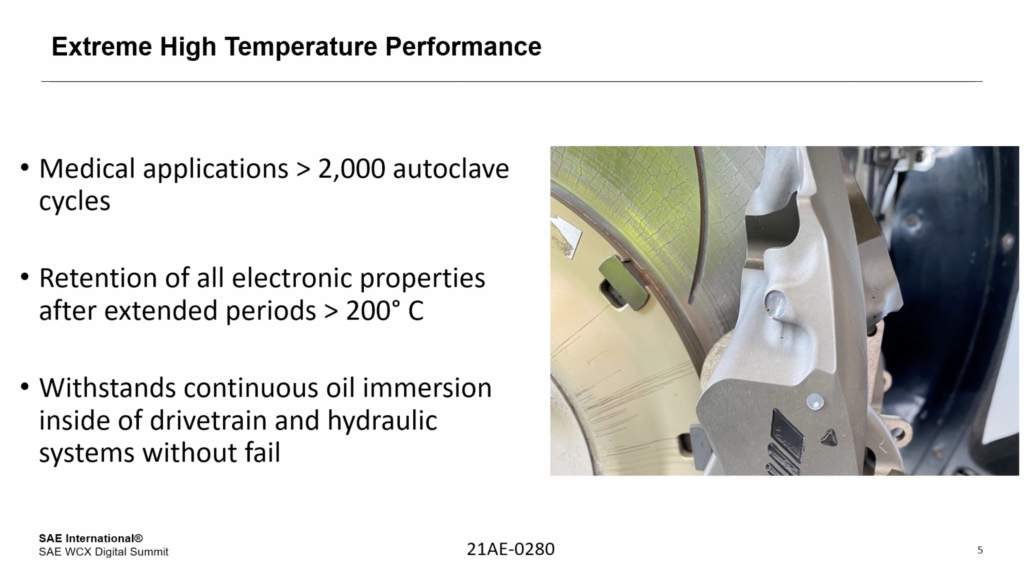
The same design parameters that are responsible for the low-temperature advantage are equally advantaged on the high temperature ranges.
The picture on the right is a disc brake assembly from a GT3 race car. The p-Chip microtransponders were attached to the disc and calipers. This picture was taken after the race. Noticed the cracking on the disk face as a result of the extreme heat generated during the race. The p-Chip microtransponder survived on the disk as well as on the calipers.
Direct-to-metal attachment is accomplished with adhesives and tapes. Due to their inner nature, they can be immersed inside of housings containing oil- and detergent-laden fluids without failing. p-Chip micro transponders readily withstand thousands of cycles of wet autoclaving at 120 degrees Celsius.
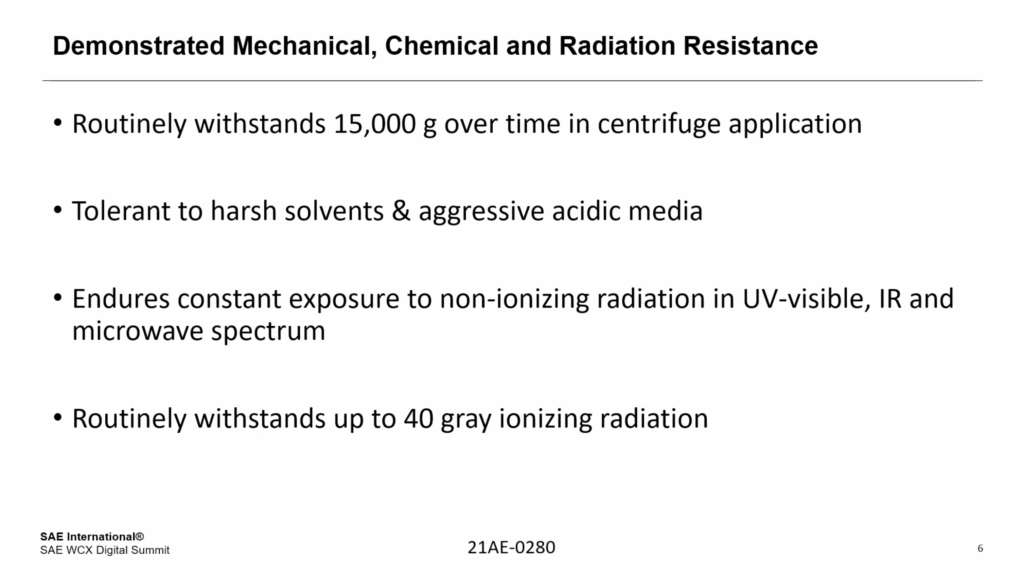
The p-Chip microtransponder is a solid-state monolithic inorganic structure. There are no moving parts to misalign, wear, or fail. The surface is covered by layers of silicon dioxide and silicon nitride, giving an exceptional resistance to strong acids and corrosive media.
Only materials that destroy glass can penetrate the p-Chip microtransponder and cause any damage. This is really limited to things like exceptionally strong bases and concentrated solutions of hydrofluoric acid.
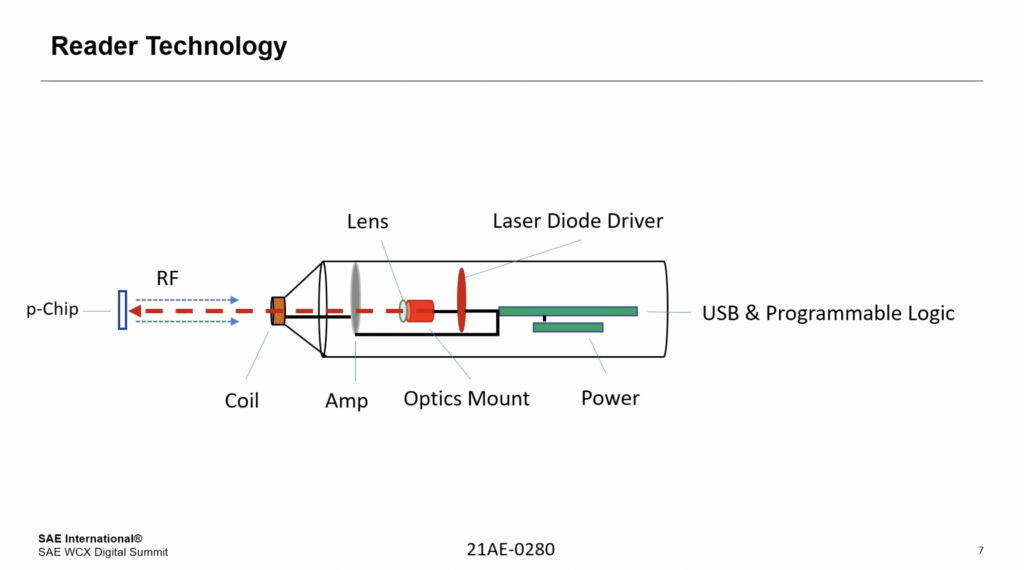
This diagram outlines the major components of a p-Chip Reader. Power is provided by hard wiring for static readers or through USB cable for portable and handheld readers. A modulated laser or laser diode is powered and controlled inside of the reader. The vast majority of applications using class three are lasers which are very affordable and safe.
The low energy radio frequency signal emanating from the p-Chip microtransponder is received by a tuned antenna coil just inside the nose of the wand. The RF signal is then amplified and shunted to the onboard logic, where it’s decoded. The decoded signal exits to the reader through the USB cable and displays the unique serial ID of the p-Chip microtransponder in software on the connected device. Read time is about 2 microseconds. The p-Chip microtransponder serial number that shows up in the software has actually been read 8 times to verify the exact number.
This is done for high speed packaging lines.
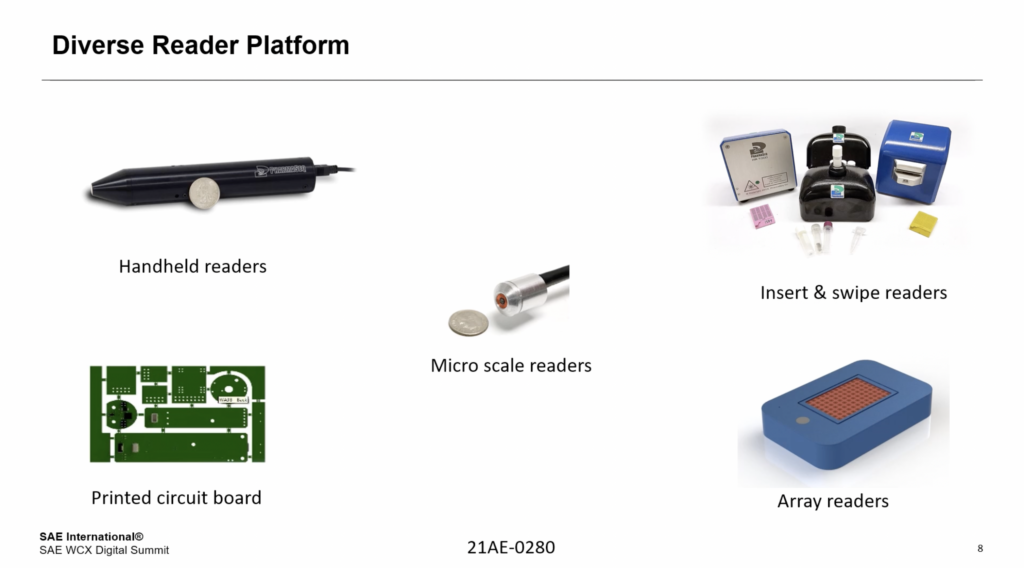
The wand reader components reviewed in the previous slide can be implemented in a wide array of form factors, including insert, swipe, and pass-under formats. The readers can be miniaturized and placed inside of machines, printers and diagnostic equipment. Reader modules for robotic arms and gantry mounted systems have also been made. Array readers capable of ingesting 96 p-Chip microtransponders in a flash have also been made to cover high volume containers and packaged goods applications.
All of the readers have the same core hardware and firmware. Data output from the readers is accomplished by open source file structures that can be easily ported into data lakes, trust centers, ERP, cloud and distributed ledger systems. We are technology agnostic.
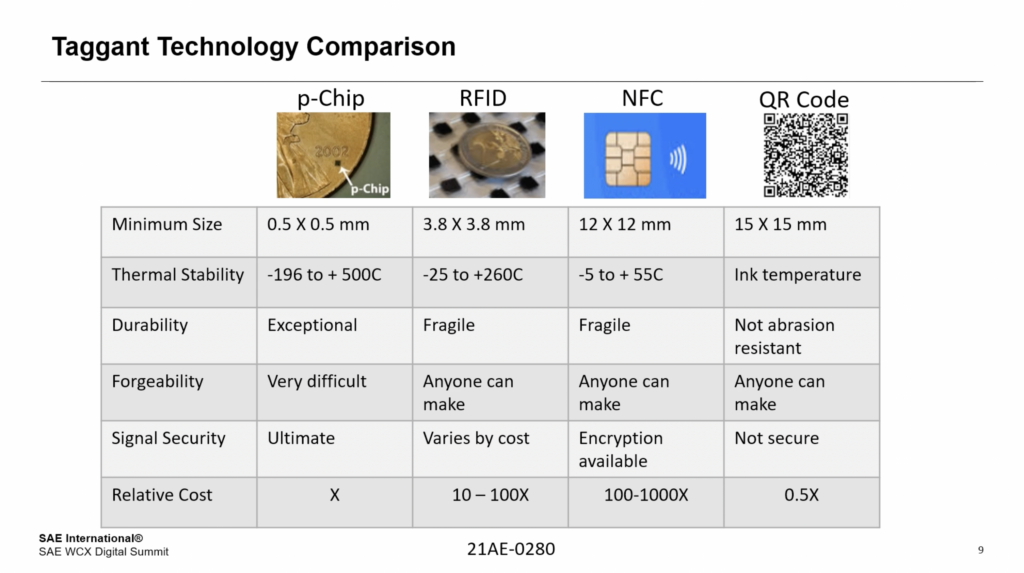
So at this point, many people are probably wondering if this is just a really, really small RFID.
No, a p-Chip microtransponder is not an RFID. This slide is intended to be a reference for you to compare some commonly used tagging technologies against optical microtransponders. I’m not going to read it. But it clearly shows some performance, security, size and cost benefits of this new technology.
While it is different and advantaged, it’s not exclusive. So p-Chip microtransponders can be used synergistically with other forms of security tagging systems as well. They work with RFIDs and NFCs and QR codes.
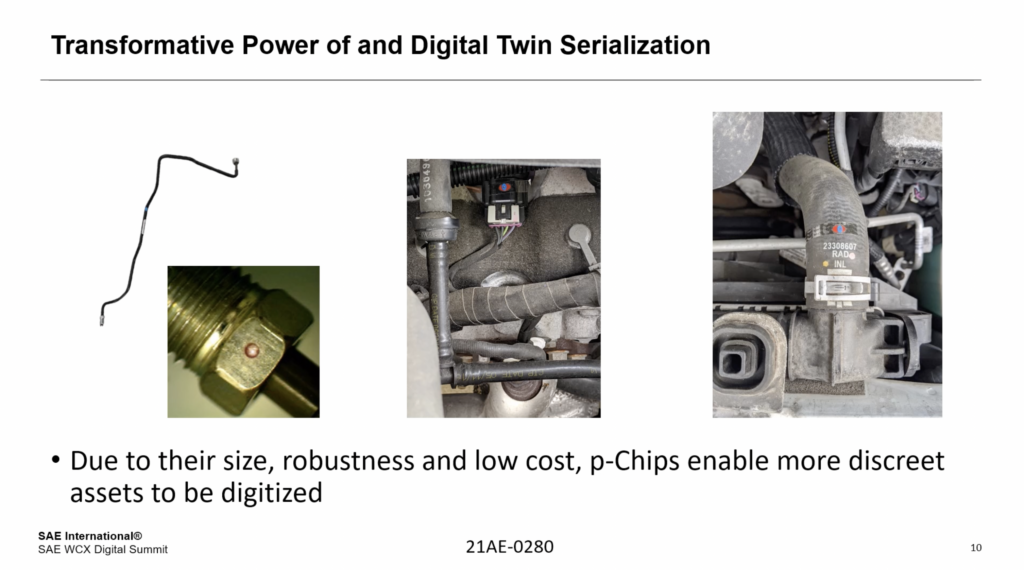
When you place a p-Chip microtransponder on a physical object, you create a digital twin of the physical object. The data associated with the digital twin can move ahead of the physical object. When you start to index data of multiple digital twins, you get massive power and intelligence.
p-Chip microtransponders can be attached directly to metals and ceramics by industrial adhesive technologies and labels. They can be melt-fused into plastics and composites easily, as well as laminated into composites, safety glass and touchscreens.
So the technology enables more objects to be tagged and transparently tracked than ever before, closing the loop on complete asset digitization initiatives. discrete components sterilization and indexing expedites root cause analysis. Affordable, component-level tracking begets data visibility and improved performance, all while reducing liability and cost-to-serve for warranty and claims.
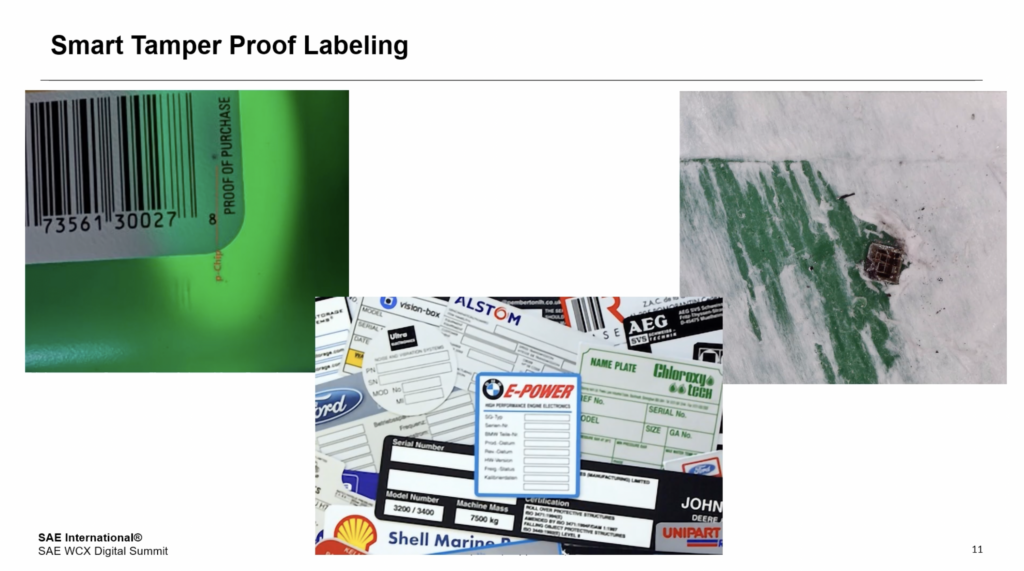
As an anti-counterfeiting technology, there is a lot of innovation that goes into labeling. Multiple patents cover the use of optical microtransponders in labels, extrusion, and laminate structures to make secure, tamper-proof, smart labels with p-Chip microtransponder embedded. Our IP portfolio includes
- in low labels secured by p-Chip microtransponders
- blow-molded structures, like oil bottles, secured by p-Chip microtransponders
- labels and containers secured by multiple p-Chip microtransponders
- combinations of P chips and printed 2d codes, barcodes, and QR codes
- self-destructive p-Chip microtransponders that fail when removed from an object or when the label is peeled, so that the chip can’t be reused and can’t be stolen, or the bottle or plastic container can’t be used by counterfeiters to put fake goods inside.
The picture on the left shows a p-Chip microtransponder embedded into a blow-molded HDPE oil container. The chip is only visible by backlighting the empty container. The picture on the right shows the same chip that was destroyed while attempting to remove it from the container. We attempted to remove hundreds of p-Chip micro transponders from these HDPE bottles. Every one of them were destroyed before the label was fully removed.
So let’s take a high-level look at what can be accomplished at the discrete part level, using a hydraulic brake system as an example.
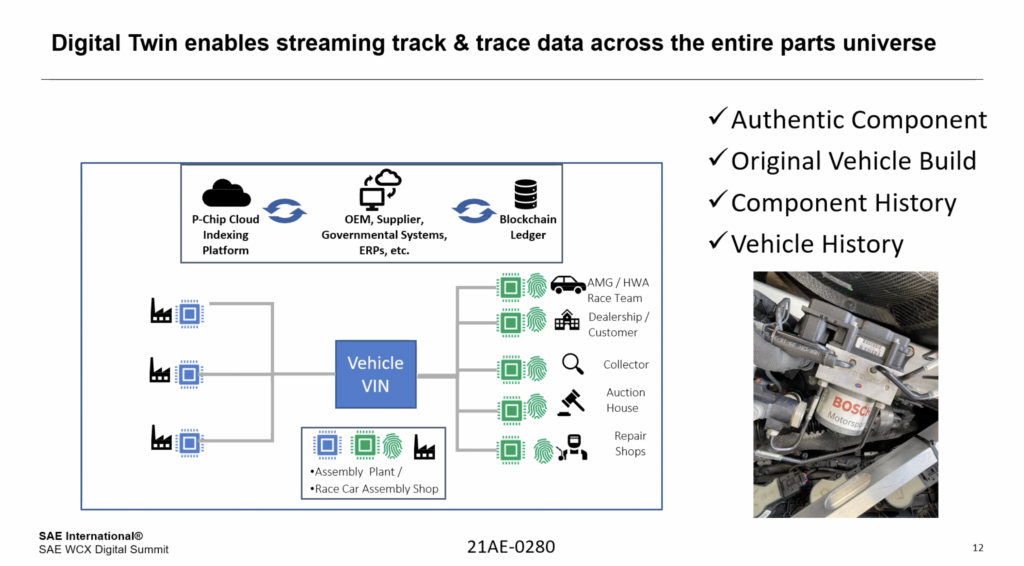
So in the graphic, the 3 plants on the left of the diagram represent multiple-tier suppliers of let’s say hydraulic brake pumps, brake lines and master cylinders, respectively. There’s no limit to the number of suppliers that can be digitally indexed.
While all 3 of the parts are manufactured at different sites, their digital ID is set at the time of individual component manufacturer. When they’re shipped to the plant in the center, the digital ID, and all the associated material-process and quality information, is transferred to the OEM assembly line.
The parts can be kitted and sent to work zones for installation on the vehicle. At the time of installation on the vehicle, the VIN numbers are read, the chips are read, and all the data is uploaded and then archived as a digital record.
The digital record coming out of the vehicle identification number can be stored in many forms, as indicated in the top of the graphic. The data can be made available inside a network for free, or can be made available via subscription for people outside of the network.
Time, date, quality and provenance of each hydraulic pump, each brake line and each master cylinder produced in this example, can be verified instantaneously by any of the users depicted in green on the right side of the graphic. The same discrete part traceability to VIN number can now be accomplished for virtually any critical safety component on a vehicle.
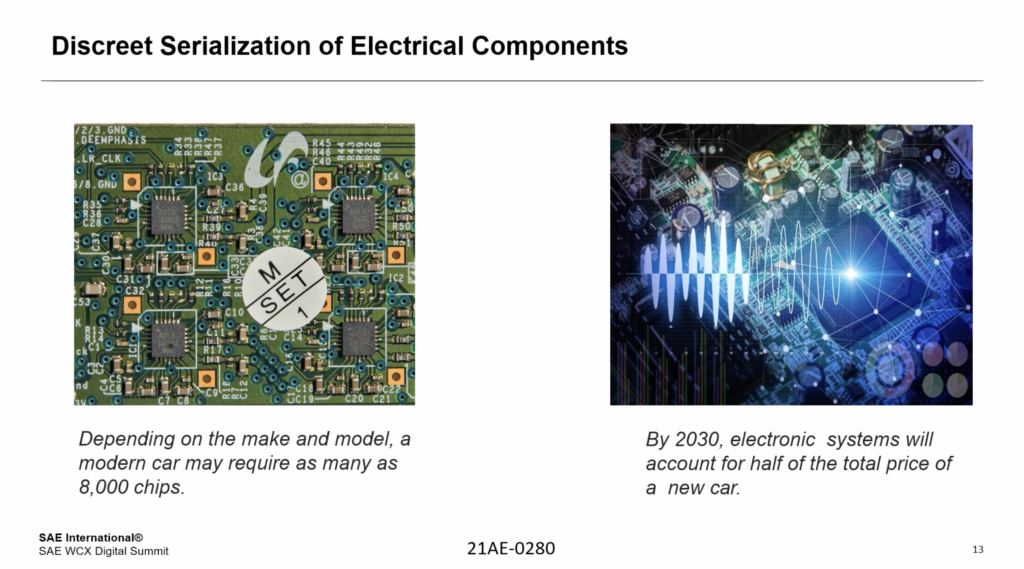
The path towards autonomous mobility and the requisite electronic components to achieve the goal is well documented. Counterfeit electronics and part failures are now leading the warranty-claim category. A large portion of the cost of non compliance can be mitigated by affordable serialization of electronic components.
Take a look at the picture on the left. You have a chipset; there are 4 chips in the chipset. Right now, it’s secured by a sticker that’s not very secure. Also, on each of those 4 chips, what you see is a number, and that number says it has these specifications. It says all 4 of those chips are the same.
But in reality, we know they’re not. If you look very closely at the bottom chip on the left, there’s a small square on it. There’s a p-Chip microtransponder there. So when you attach a p-Chip microtransponder to an electronic device, you have the ability now to give it a unique serialization—instead of a code that takes you to a table that tells you the specs that this chip should be capable of passing.
Because p-Chip micro transponders are themselves high-performance integrated circuits, they’re perfectly capable of surviving the thermal cycling from electronic components without loss of properties themselves.
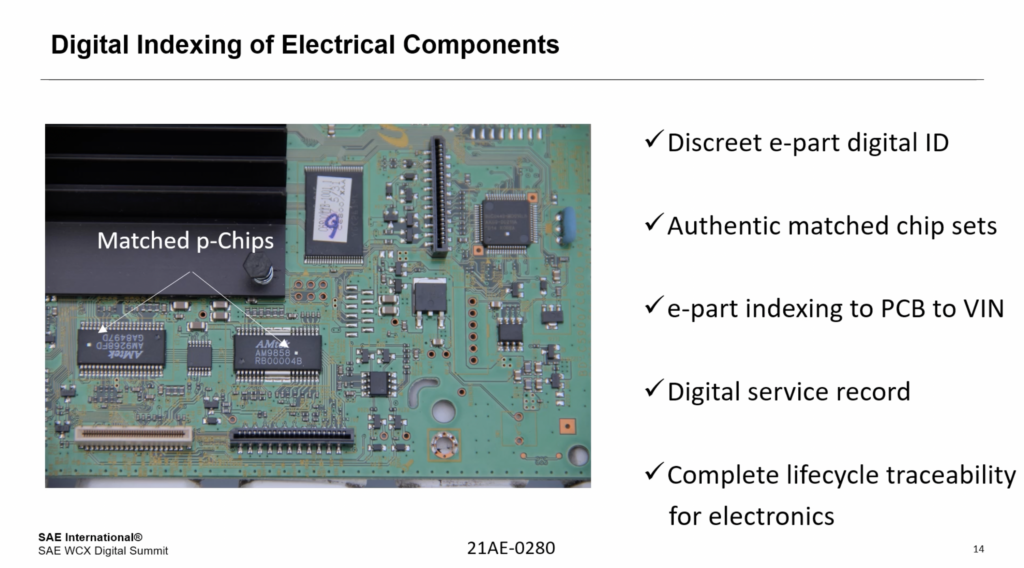
Similar to the brake system example earlier, we can index multiple electrical components on a PCB, multiple PCBs to a device and a device to a VIN number. We can even attach them directly to other integrated circuits individually, and then index them together as chipsets on a device.
Once discrete electronic components have a unique unclonable serial ID, it’s possible also to have a digital CMA that maps to the individual electronic component. In spec, or subs, substandard chips are digitally marked. They can be identified in a distributed ledger.
Substandard and counterfeit components are easily identified, along with the people or attempting to sell them. An entire digital service record for critical safety components can now be deployed.
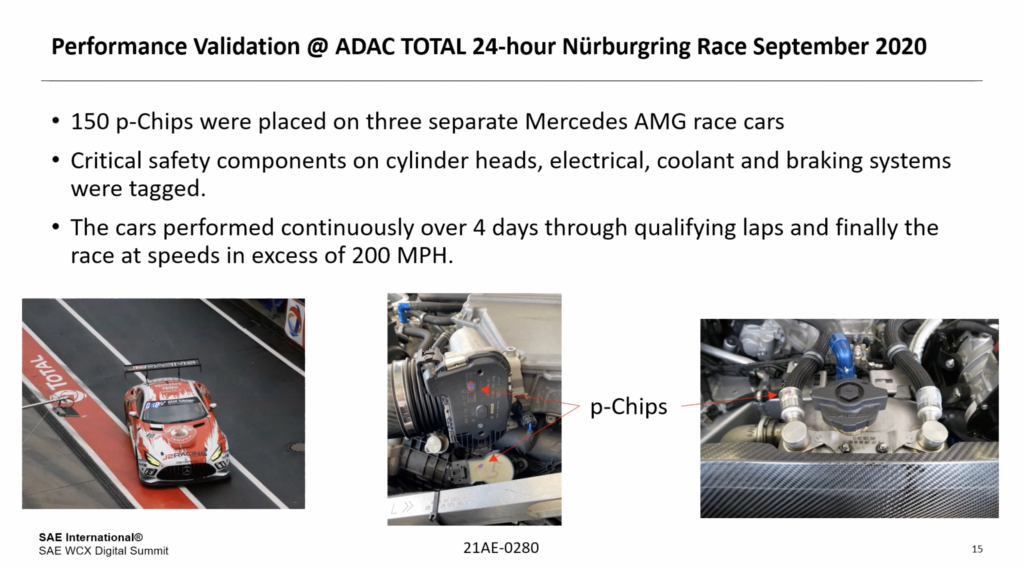
The ADAC total 24 Hours of Nürburgring race is a world renowned endurance race In partnership with Germany, p-Chip microtransponder were placed on 3 Mercedes AMG race cars to demonstrate extreme automotive performance capability. 150 chips were placed on critical safety parts to validate attachment methods, we would ship castings, machined metal, ceramics and composite structures. Components were also chosen to have maximum exposure to temperature cycles, wind and rain. Once attached, the PE chips could not be accessed until after the race ended.
Over 4 days, the chips performed exceptionally well. This year’s race included extended periods of high winds and driving rain, which multiplied the environmental forces on the components and the p-Chip microtransponders.
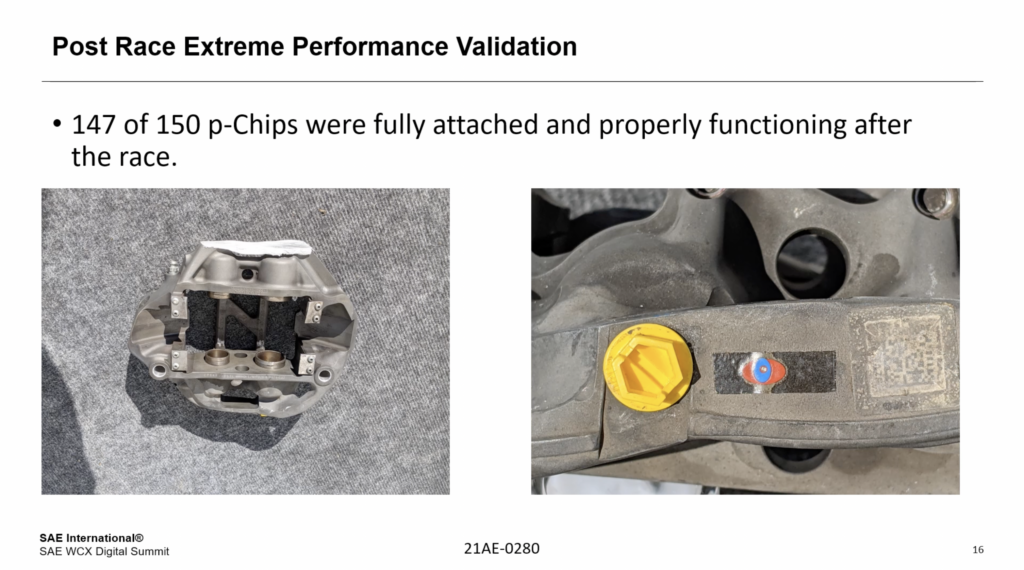
At the end of the race, 147 of the 150 p-Chip microtransponders attached to the cars were in place and functioning perfectly after the race. So you’re thinking about what happened to the other 3. Those chips weren’t read because they were on parts that were shunted right back to the manufacturers during the race; we didn’t have an opportunity to read them.
So the pictures on this page are different views of the same brake housing.The brake housing was damaged badly during the race. In the top-left picture, you can see the metal has been melted due to the friction caused by a collision. On the right-hand side shows a p-Chip microtransponder. It’s attached directly to the casting with a thermally activated tape laminate; and it also shows a QR code next to it. The P chip is still functioning; the QR code was distorted by heat and is no longer readable.
The race results clearly demonstrate the extreme performance capabilities and durability of this new digital tagging technology. The results give us confidence that p-Chip Corp. technology has the ability to meet and exceed performance specifications for all forms of transportation, from light-duty vehicles to heavy-duty trucks and buses.
If you’d like to learn more about the race, or if you’re just interested in speed, take a look at the brief video from the race.
I’m always motivated to have open dialogue with open-minded collaborators who have a bias for action. Please contact me if you’re of like mind.
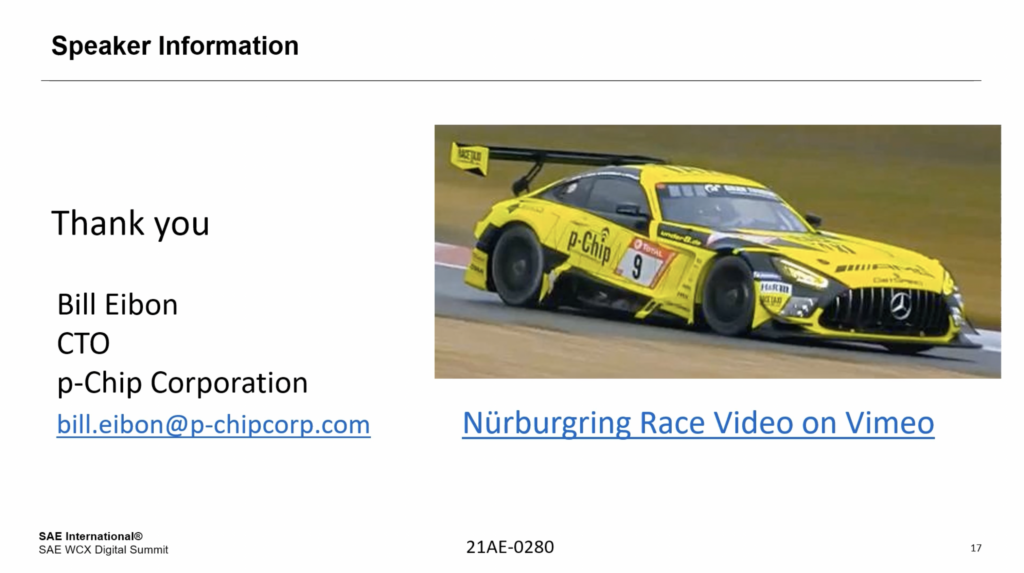
Leave a Reply